News & Events
Surface modification method and analysis of modification effect of alkaline zinc carbonate
2022-10-17
Surface modification method and analysis of modification effect of alkaline zinc carbonate
Alkaline zinc carbonate has a large specific surface area and small particle size, which makes it easy to mix together. It is also not easily dispersed uniformly in organic media, which reduces the performance of alkaline zinc carbonate. Therefore, specific powder modifiers are needed to modify the surface of alkaline zinc carbonate to achieve uniform dispersion in different organic media. It is widely used in rubber, inks and coatings, glass ceramics, optoelectronics and other fields. So how many surface modification methods are there for basic zinc carbonate?
1. Powder Surface Coating Modification
Currently, the common surface modification method for ultrafine inorganic powder fillers is to use powder modifiers to coat the surface of the particles to give new properties to ultrafine alkali zinc carbonate and improve the application performance of downstream products.
Application methods.
(1) Wet process, where the powder is first added to the organic medium, then the powder modifier is added and the activation index of the alkaline zinc carbonate is increased by stirring or ultrasonication for more than 90min to achieve uniform dispersion in the organic medium for rubber, plastics and coatings.
(2) Dry process, through the grinding equipment bin, equipped with powder modifier, through the coating modified grinding, in the production of alkaline zinc carbonate in the process of surface modification has been done, can greatly improve the cost and downstream product performance.
2. Mechanochemical studies on the surface modification of alkaline zinc carbonate
The surface of the particles is activated by crushing the ultrafine powder by mechanical force, thus changing its surface crystal structure and physicochemical structure. In this way, the molecular lattice is displaced, the internal energy increases and the surface of the activated powder reacts and adheres to other substances under the action of external forces, thus achieving surface modification.
3. Precipitation method for surface modification of nanopowders
In this method, a coating is precipitated on the surface of the particles with organic or inorganic substances to modify their surface properties. In-situ coating of Al2O3 in the preparation of ZnO precursor alkaline zinc carbonate. reduces the process of multi-particle agglomeration and improves the coating effect compared to conventional surface coating processes. The particle size of the coated ZnO composite powder is approximately 50 nm and the coating layer is 3-5 nm. the photocatalytic activity of the thickly coated alkali zinc carbonate is significantly reduced, but its good UV adsorption properties are ensured.
There are many different methods of modifying alkaline zinc carbonate, which need to be achieved according to their own and the basic conditions of the effect that they want to achieve, but modifying ultrafine powders is the trend in the industry, because this way not only can improve the performance of the original ultrafine inorganic powder, but also can improve the performance of downstream products, opening up more markets and new applications.
Latest News
Talk to us about your needs

Contact Hotline
Mobile:+86 13806148496
E-mail:kmciwh@163.com wanghao@bluestargtc.com
Address: No.99, Danyangmen North Road, Jintan District, Changzhou City, Jiangsu Province
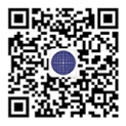
【WeChat Public】
Copyright 2023
Jiangsu Bluestar Green Technology Co., Ltd Powered by www.300.cn Tags
Copyright 2023 Jiangsu Bluestar Green Technology Co., Ltd Powered by www.300.cn Tags